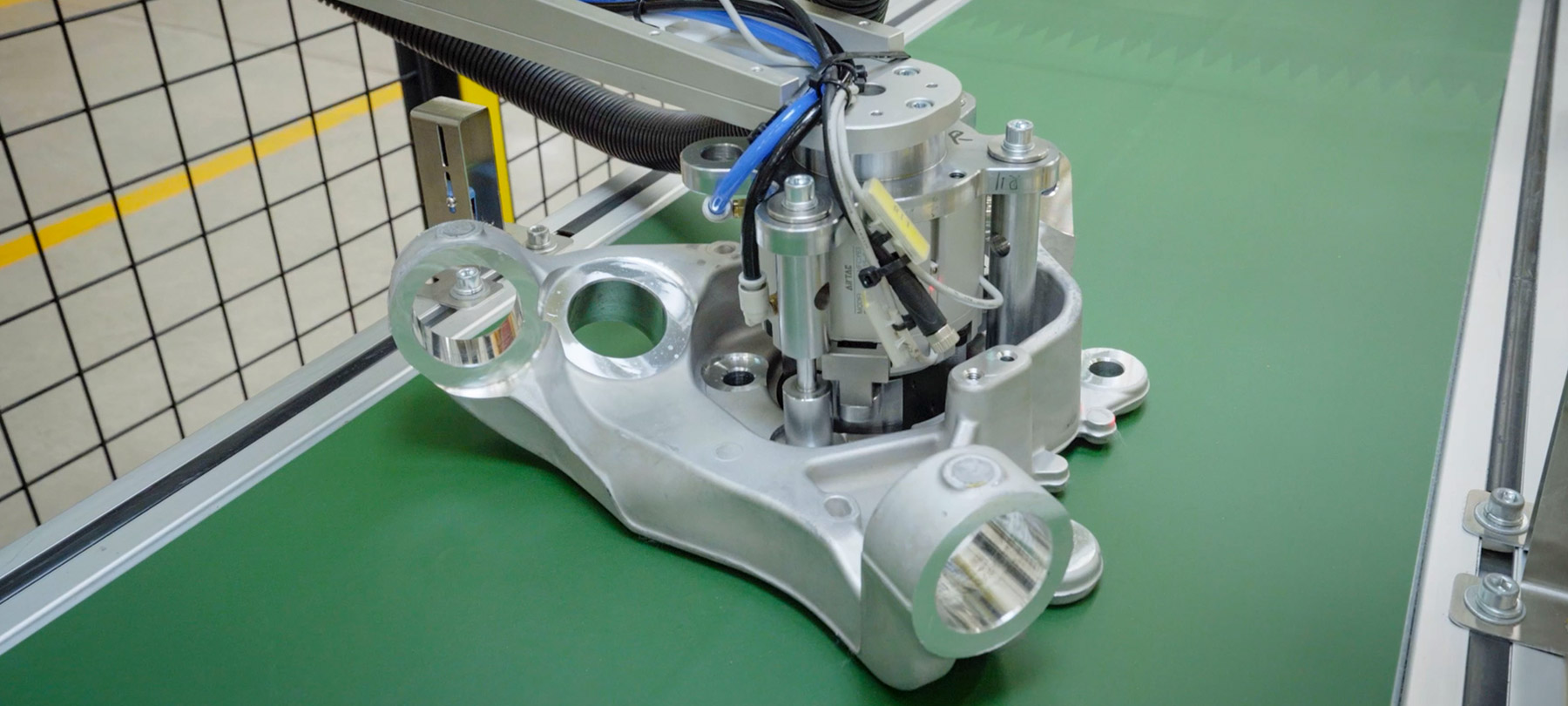
Flexible and Reliable
Die Casting Solutions
In die casting, the melt is pressed into a mold under pressure, where it solidifies. This process achieves a high casting quality despite the high speed at which it is performed and is especially suited to thin-walled parts. Die casting is used primarily in the series or mass production of structural parts.
BBS provides automatic casting equipment and post-processing lines for castings, including automated loading and unloading of casting machines, casting cooling, vibrating device for sand removal, coding, deburring, sawing and drilling, flow detection, X-ray/CT inspection, etc.
Your Personal Contact for Foundry Automation
You are interested in professional foundry automation solutions for your application?