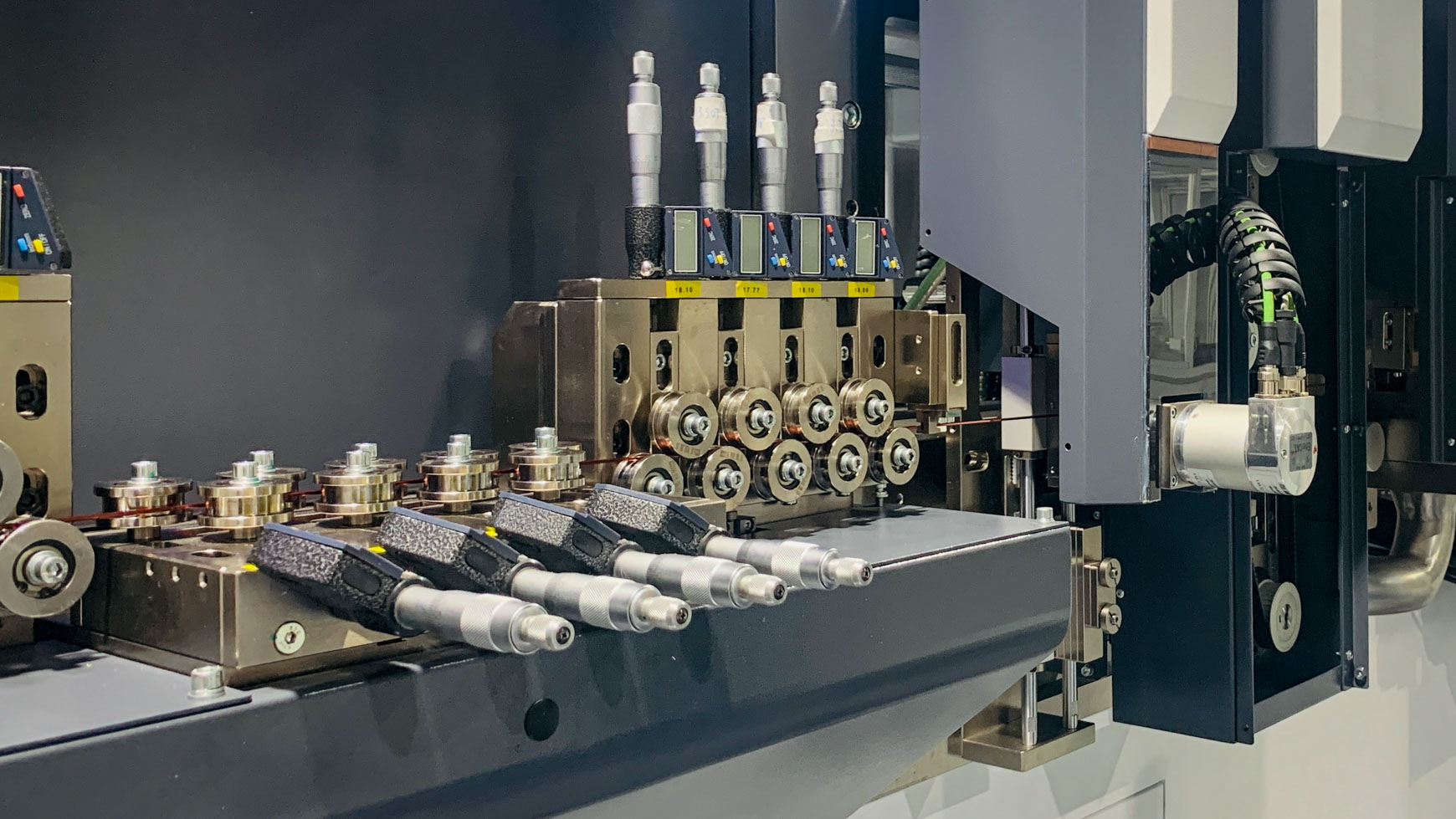
A Maximum of Reliability and Modularity
Stators with hairpin technology are used in connection with the manufacture of electric drive motors (traction motors) for electric vehicles, both passenger cars and commercial vehicles. This technology is becoming increasingly important as the transport revolution progresses and more and more vehicles get electrified in almost all countries.
Hairpin technology belongs to the winding processes, although no conventional coils of copper wire are manufactured. Rather, copper bars are used, which are inserted into the stator stack and consist of enameled copper wire with a layer of lacquer. The U-shape of these plug-in coils is reminiscent of classic hairpins. Due to the flat cross-section of the copper wire, the slot fill rate of the hairpin can be higher, which means better power density. In addition, the high fill rate also results in better thermal performance and NVH.
The BBS production machines for the manufacture of hairpin stators are characterized by a specific structure, they are designed for the production of large quantities. They represent the entire process chain:
The individual process steps run in individual process cells. These are available as standalone or complete solutions.
See our winding technology section for roving, needle and linear winding technology.
Wire forming
Paper Insertion
Wires insertion
Widen
Twisting
Welding
Are you interested
in professional hairpin technology for your application?